Mantenimiento predictivo en minería eléctrica
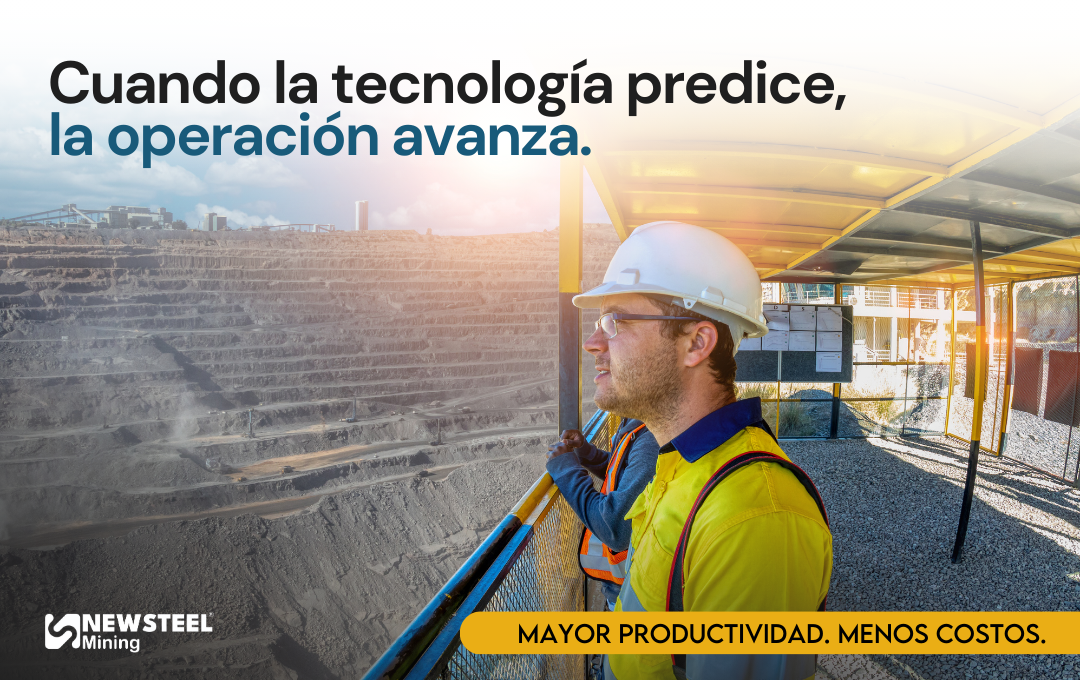
La transformación de camiones diésel a 100% eléctricos a batería en minería ha elevado la complejidad técnica de las operaciones. Garantizar la disponibilidad y la eficiencia de estas flotas exige nuevas estrategias, siendo el mantenimiento predictivo una de las más efectivas. Esta metodología permite anticipar fallas, optimizar recursos y proteger la inversión realizada en la electrificación de los equipos.
El monitoreo de variables críticas para anticipar fallas
El mantenimiento predictivo se basa en el monitoreo continuo de las variables técnicas que determinan el estado y desempeño de cada sistema del camión eléctrico. Este monitoreo se realiza mediante sensores instalados en puntos estratégicos que envían datos en tiempo real a plataformas de análisis.
Las principales variables monitoreadas son:
- Temperatura de operación de motores eléctricos y sistemas electrónicos.
- Niveles de vibración en ejes, reductores y rodamientos.
- Consumo energético y eficiencia en cada ciclo de trabajo.
- Ciclos de carga y descarga de las baterías y su salud.
- Desbalance de celdas y resistencia interna en las baterías.
Este monitoreo no solo detecta fallos inminentes, sino que permite comprender cómo cada componente responde a las exigencias diarias de la faena.
Trazabilidad técnica: Cómo se construye y su valor en la operación
La trazabilidad se construye al registrar y almacenar cada uno de los datos operativos durante el ciclo de vida del camión. Cada sensor alimenta un historial técnico que permite:
- Identificar patrones de desgaste o anomalías.
- Relacionar fallas con condiciones de operación.
- Planificar intervenciones según la condición real y no por calendario.
Por ejemplo, si un motor de tracción muestra temperaturas superiores a su rango, la trazabilidad permite decidir la acción a tomar sin esperar al próximo mantenimiento programado.
Este proceso reduce errores en la toma de decisiones, evita detenciones innecesarias y maximiza la vida útil de activos como las baterías.
Impacto técnico y económico en la productividad minera
El mantenimiento predictivo impacta directamente la productividad y costos de la mina. Su aplicación va más allá de prevenir fallas: permite mantener la producción incluso en condiciones exigentes.
Ejemplos de impacto:
- Detectar caídas de eficiencia en el frenado regenerativo y ajustar a tiempo.
- Anticipar la pérdida de autonomía de una batería para evitar detenciones.
Además, permite:
- Reducir inventarios de repuestos innecesarios.
- Optimizar la utilización de los camiones.
Esto se traduce en una mayor disponibilidad operativa de las flotas, reducción de los tiempos muertos y un uso más eficiente de los recursos, generando ahorros en costos de mantenimiento y mejorando la capacidad de cumplir con los planes de producción.
El rol de la remanufactura en la extensión de la vida útil
Identificar el desgaste real de los componentes habilita procesos de remanufactura controlados. Conociendo el historial de cada pieza es posible decidir cuáles pueden reacondicionarse y reutilizarse con seguridad.
Ejemplo: módulos de batería con desgaste controlado pueden reconfigurarse para seguir operando, mientras otros se retiran planificadamente.
Esto reduce costos de reposición y la generación de residuos, aportando a la sostenibilidad de la operación. Muchas mineras ya aplican estas estrategias, como se detalla en la remanufactura en minería.
Maximizar la disponibilidad de flotas eléctricas 100% a batería
En el caso de las flotas eléctricas 100% a batería, el mantenimiento predictivo se vuelve aún más relevante debido a la naturaleza del sistema. A diferencia de los equipos diésel, estos camiones no cuentan con sistemas auxiliares que permitan continuar la operación ante una falla mayor. Cada detención impacta directamente la producción y la planificación logística de la mina.
Aplicar esta metodología permite:
- Asegurar la continuidad incluso en turnos extendidos.
- Prevenir sobrecargas y fallos eléctricos.
- Extender la vida útil de las baterías.
NewSteel lidera la transformación de camiones diésel a 100% eléctricos a batería en Latinoamérica, entregando a las mineras la posibilidad de operar con flotas más eficientes, seguras y preparadas para los desafíos actuales de la industria.
Si quieres conocer cómo esta tecnología está cambiando la operación minera y cómo implementarla en tu proyecto, contáctanos a través de Instagram, en LinkedIn o escríbenos directamente por WhatsApp.